Cycle Time Formula: Learn How to Calculate it with Examples
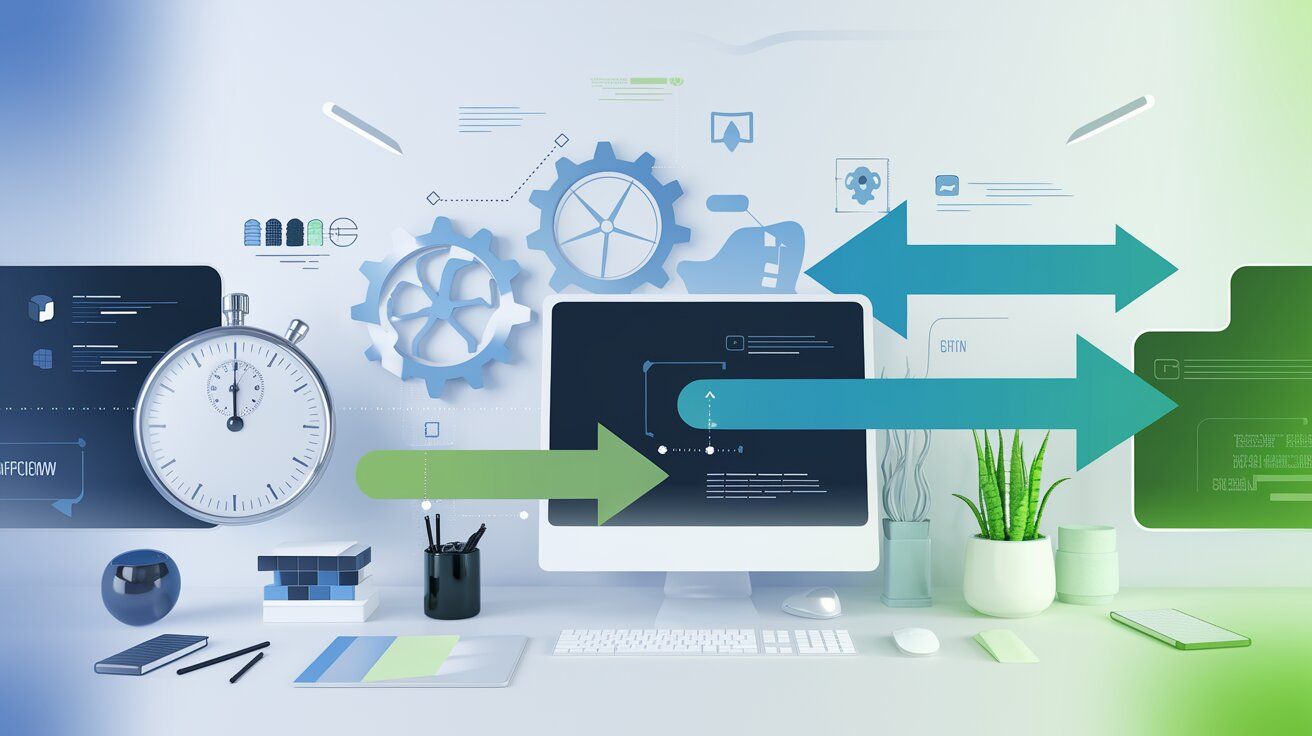
Cycle Time Formula is wonderfully helpful when it's about getting your job done on time.
It's a very simple equation that helps you identify your business's slowdowns and get things moving faster.
Like myself, if meeting deadlines is your thing, just use this formula. It lets you keep your workflow flexible, so you can always deliver on time. That said, I’ll break down —
- What is cycle time?
- How you can calculate it
- Advantages and challenges of using cycle time
- Who needs to calculate it
So, let’s explore!
What is Cycle Time?
Cycle time is the amount of time it takes to finish a task from beginning to end. By optimizing cycle time, you can greatly increase productivity and efficiency. It's mainly a time management concept that was first coined in lean manufacturing.
When you grasp and improve cycle time, it can change how you manage manufacturing teams, business operations, projects, and the supply chain. Though it might seem simple, cycle time is vital for tracking team productivity and overall performance.
It goes beyond just output and materials. By accurately measuring cycle time, you can monitor task duration and labor costs effectively.
Now, to calculate the right cycle time, you must have the right tracking tools, like Apploye. It can show how long your team spends on each task, from start to finish.
Start Calculating Cycle Time with Apploye!
Cycle Time Formula
To find cycle time, you have to divide the total production time by the number of units produced. The formula is —
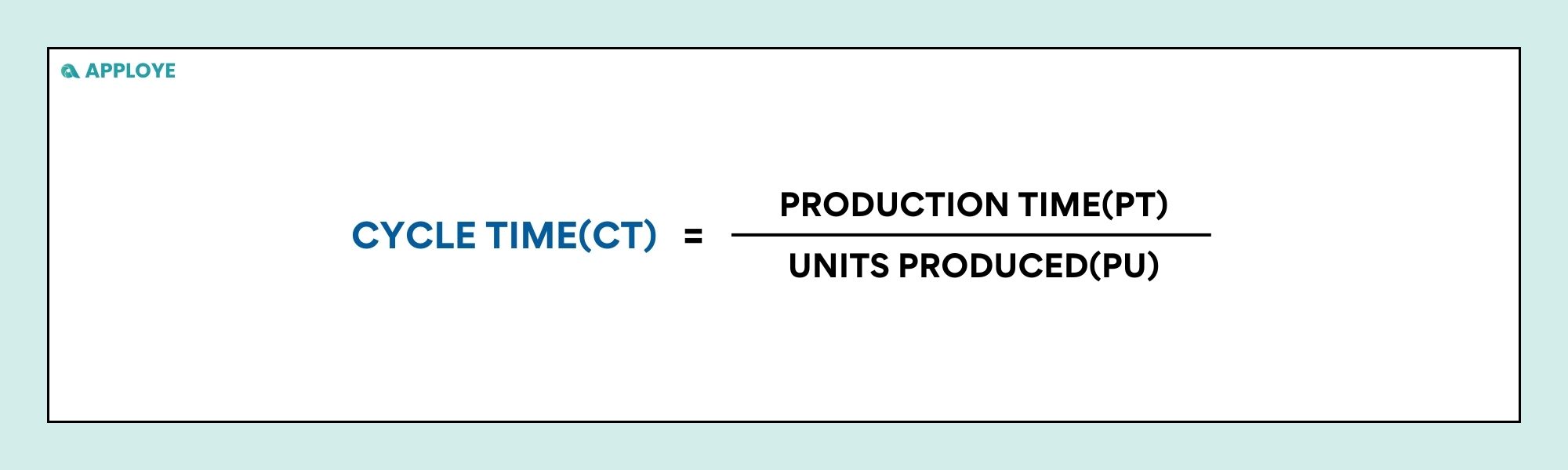
Example
Suppose you run a marketing agency. Your agency spends 30 hours a week to produce 60 ads. It means —
So, your agency produces one ad every 0.5 hours or 30 minutes per ad. Hence, the cycle time for creating an ad at your agency is 30 minutes.
What are the Challenges of Calculating Cycle Time?
Calculating cycle time has many advantages. However, you can find it tricky to do it accurately. From time to time, various issues can arise, making the process challenging.
Now, I’ll share with you a few challenges. That way, you can identify and manage these obstacles.
- Communication Silos: If team members fail to collaborate effectively, your project workflow can be hampered.
- Lack of Task Prioritization: When you manage numerous tasks simultaneously, it's difficult to focus efforts efficiently.
- Disrupting Distribution and Supply: When you adjust cycle times, you must consider their impact on supply and distribution. You should closely monitor these changes to maintain efficiency.
How to Calculate Cycle Time Formula
Here’s how I do the calculation. I take the time necessary to complete a task or produce an item, excluding any breaks.
Step 1: I ensure when a task starts and finishes, like in a project tool.
Step 2: To get precise task duration data, I use time-tracking software. I very well know how accurate data is vital for the next steps.
Step 3: Now, subtract non-productive time from the total available time. For example, if my team works 7 hours but takes 1 hour for breaks, the net production time is 6 hours.
Step 4: It’s time to use the cycle time calculation formula:
Cycle Time = Net Production Time / Number of Work Items Completed
Further Read: Benefits of Time Tracking Software
Example calculation
If my team has a net production time of 50 hours in a week and completes 20 tasks, the cycle time is:
Cycle Time = 50 hours / 20 tasks = 2.5 hours per task
Remember, an ideal cycle time should be less than 48 hours.
It usually shows the agile and responsive practices in software development. Meaning, that teams can promptly meet the requirements, supply features, and accept changes.
I fell into the “Good” rating! Well, if your team is taking longer cycle times in software development, I’d suggest you look for inefficiencies ASAP.
Otherwise, you might get broke due to higher costs and delayed delivery of features.
Application of Cycle Time Formula in Professional Services
This time, I want you to consider a marketing agency-based project.
Suppose you lead a team. You have a task to improve your company's online presence by creating more blog content.
Now, assume you have four content writers. They each take 5 hours to write a 2,000-word post. Meanwhile, you aim to publish 14 blogs per month.
As a way to figure out the cycle time for your team, you can use the process cycle time formula as follows —
Cycle Time = 5 hours / 1 blog post totaling 2,000 words
It means the cycle time is 3 hours per blog post. To calculate the total time needed to produce 16 blog posts, multiply the cycle time by the number of posts:
5 hours x 14 blog posts = 70 hours
Thus, it’ll take the team 70 hours to complete 16 blog posts. You can now schedule blog production hours into your team's workflow. It ensures efficient time management and better content alignment.
Similar Read: Excel Timesheet Formula
Application of Cycle Time Formula in Production Settings
Suppose you’re starting a small business making handmade candles. To price your candles correctly, you need to know how many you can produce in a given period.
You work a 7-hour shift with a 1-hour break, resulting in a net production time of 6 hours. Today, you made 30 candles. Using the cycle time formula calculator, you can find out the cycle time —
Cycle Time = 6 hours / 30 candles
So, you can produce one candle within 12 minutes. Now, you can use this cycle time to calculate labor costs and add them to material expenses to ensure profitability.
Suppose you pay an hourly wage of $20.
- Hourly Wage: $20
- Minutes per Candle: 12
- Wage per Minute — 20 / 60 = $0.33
So, Labor Cost per Candle: 12×0.33=$4
Now, if you add material cost per candle of $2, then you get a total cost that is —
Labor cost $4+ Material cost $2 = Total price per candle is $6
To ensure profitability, you need to price each candle above $6.
Tip: I regularly monitor and adjust cycle time to refine my pricing model and improve efficiency. You should try it!
Application of Cycle Time Formula in Delivery Services
Let's explore how cycle time works in a delivery service context. Imagine you work for a courier company and handle the daily delivery routes.
You operate —
- A 9-hour shift
- A 45-minute lunch break
- A 15-minute break
Removing breaks, your net production time is 8 hours.
During the 8-hour production time, you delivered 160 packages. Using the delivery cycle time formula, you can calculate —
Cycle Time = 8 hours / 160 packages
In this case, it takes 3 minutes to deliver each package. With an efficient cycle time, you can plan and optimize delivery schedules.
Besides, you should apply the cycle time formula in operations management to ensure better productivity.
Further Read: 9/80 Work Schedule
How Do You Calculate Cycle Time Without Non-Working Hours?
When a customer places an order, they care about how long it takes them to deliver the desired product. Well, that’s what you and I call the total cycle time formula.
Suppose, your average delivery time is 5 days. It’s based on historical data excluding weekends and non-working hours. However, this calculation doesn’t consider weekends, so the actual delivery time becomes 9 days.
Now if I were your customer, it surely wouldn’t be a pleasant experience for me to wait such long. In some cases, companies exclude non-working hours to show shorter delivery times.
All-in-all, accurate calculation of cycle times keeps customers happy. You see, by using the right cycle time formula in operations management, you can improve customer satisfaction.
How Do You Calculate Cycle Time Including Non-Working Hours?
You can satisfy or exceed customers by including non-working hours, such as weekends.
For example, if you promise a customer on Thursday that you’ll complete a task in 6 days. So, they’ll expect it by the following Wednesday.
By using the total cycle time formula and including weekends, you can meet customer expectations.
Calculate Cycle Time Excluding Holidays
Let's say you have a team in the U.S. and another in Japan working together on a project. Both countries have different holidays.
So, you must exclude them from your cycle time calculations.
Using remote employee monitoring tools, you can define and exclude these holidays.
For instance, if the U.S. team has July 4th off and the Japan team has a holiday on August 11th, these days won't count in your cycle time.
This way, you ensure accurate cycle time calculations and meet customer expectations.
The Benefits and Role of Cycle Time
Cycle time is important for measuring process speed and efficiency, just like lead time and TAKT time. It offers significant benefits to both organizations and projects.
Some of the major benefits I’ve experienced are —
Cost-savings Increasing Profits
When you optimize cycle time, you cut costs and increase profits. And it’s obvious if you know how your time is used, you can identify areas to improve.
For example, one company increased its pretax profits from 2% to 13%. How? They focused on analyzing cycle time alongside other lean principles.
That’s why, I use a time tracker with screenshots to improve time management and further reduce costs.
Efficient System Setup
Along with increasing profits, you can bring process efficiency better by knowing your cycle time. In lean manufacturing, it helps you arrange the production floor with the right number of tools, machines, and personnel.
By any chance, if you see your time cycle is longer, you can easily tweak it to simplify operations. Here, you can apply the cycle time formula in manufacturing to ensure optimal efficiency and productivity.
Further Read: Productivity vs Efficiency
Identify Potential Improvements
You can find improvement areas while monitoring cycle time. Well, I was happy since my operation cycle time was good enough.
But there were still delays.
And I solved problems like machine downtime or material shortages by focusing on this cycle.
So, you should regularly check cycle time to spot changes and adjust as necessary.
Improve Production Consistency
Without a steady production rate, you can lose your flow rate. In that case, cycle time helps you to keep track and improve the flow.
Besides, when you standardize the production rate, you can avoid underproduction and overproduction.
Hence, your operations become more efficient.
Increase Team Productivity
When you analyze cycle time data, you uncover inefficiencies in your team’s workflow. For example, if you notice slow delivery times, you might increase the production batch size for a quicker turnaround.
So, understanding cycle time is crucial. It helps you identify and implement improvements that ultimately increase workplace productivity.
You can easily track time, figuring out where you and your team spend each minute with Apploye. Assign tasks, track how long things take, and deliver on time.
Want to Increase Your Productivity?
Improved Project Scoping
From my experience, knowing how long tasks take makes project planning easier and more accurate. This approach prevents frustration for both your team and customers.
Instead of speculating, use cycle time data to scope your projects precisely.
Shorter Cycles = Happy Customers
We all are customers of companies in different aspects of life. So, you and I know that faster delivery makes your customers happier. For example, I’ve seen a software team cut feature request times from a month to two weeks.
It directly improves customer satisfaction.
Better Understanding of Business Spend
Cycle time helps you understand the value of your processes. By analyzing resource usage and costs, you can focus on high-value tasks. Using a machine cycle time formula refines these insights, leading to smarter financial decisions.
Further Read: How to Stay Organized At Work
Who Calculates Cycle Time?
Mostly project managers, product managers, software leads, production heads, and suppliers calculate cycle time. It impacts business efficiency and success.
You don't have to do the math manually. There are plenty of tools that make it simple. For example, a cycle time calculator can help.
In fact, to increase my productivity even more, I use a project management tool, like Clickup. It helps me understand workflows and calculate cycle time extensively.
How Do You Reduce Cycle Time?
Reducing cycle time is key to improving efficiency. Here are some simple steps to help you get started.
Begin a Process Map
You should start by creating a process map. Even better, use a value stream mapping. This map breaks down the workflow of a part or product through the process and at each step.
If you manage data manually or use outdated procedures, you face many inefficiencies, bottlenecks, and delays. Here, a process map helps you figure out what's wrong and fix it.
Calculate Existing Cycle Times
You need to know your current cycle times before you can improve them. Even if you're using manual data, having a rough cycle time benchmark is essential. It gives you a starting point.
Manual data management often overestimates overall equipment effectiveness (OEE). That’s where getting your real cycle times can help you improve.
Removal of Waste
Once you have a mapped process and know your current cycle time, it's time to cut out waste. Common types of waste include —
- Quality issues where defective products slip through or need rework
- Non-value-added tasks
- Excessive manual paperwork or error-prone documentation
- Underproduction or Overproduction
- Inefficient material transport, staging, or machine layout
Interestingly, I managed these wastes which ultimately improved my cycle time.
Further Read: 7 Common Time Wasters in Workplace
Develop Standard Work Documentation
Once you've pinpointed problems and found solutions, keep consistency in mind. Standard work documentation shows how tasks should be done.
It includes —
- Clear steps
- Movements
- Communication protocols
- Other guidelines
Ensure everyone doing the task has access to this documentation and use it to train new employees. It helps keep your cycle time low and consistent.
Audit Machine Capacity
Manufacturers often handle a mix of simple and complex products. To manage this, you need to regularly check your machine capacity.
For instance, I ask myself, “Can I handle large orders filled with complex, time-consuming parts on each machine?”
To meet these demands, you must create flexible production plans based on current orders that optimize each machine's capabilities.
Cycle Time Best Practices
Once you've calculated your cycle time, you must keep it steady or reduce it. Here are some simple tips to help you improve productivity and lower cycle time —
- First, remember that takt time is based on customer demand and available time, so it often changes. Don't mix it up with cycle time.
- Cycle time isn't fixed. Things like supply chain issues, machinery downtime, and staff shortages can impact it.
- Make sure your data collection process is accurate. Bad data means bad results.
- Break projects into smaller parts. Track these through detailed workflow analysis to find where bottlenecks are.
- Increase your team’s performance by tracking how long tasks take. It helps reduce overall cycle time.
- Be smart with project assignments and scheduling to cut down on downtime.
- Finally, use cycle time data to reward top performers and set goals for your team.
Risks of Focusing on Cycle Time Improvements
Yes, improving cycle time helps your team. However, when you only focus on this metric, it does bring some risks.
Let's look at some of the major ones —
Ignoring Complexity and Technical Debt
Cycle time shows how long tasks take, but it doesn't account for complexity. If you just aim to shorten cycle times, your team might miss out on vital technical improvements.
In fact, it slows future work and increases maintenance costs when unfixed issues pile up.
Sacrificing Quality for Speed
Software quality can suffer if you just focus on reducing cycle time. Your team might rush to meet tight deadlines. And that leads to buggy or incomplete software.
It harms user experience and can damage your team's reputation.
Overlooking Customer Value
It's easy to get distracted by cycle time when you're too focused on it. If you prioritize speed over functionality, your software might not meet user requirements.
Moreover, it can lead to lower customer satisfaction and lower adoption rates.
Neglecting Collaboration and Learning
When you focus on cycle time too much, it can hurt team learning and collaboration. In fact, too much focus on finishing tasks quickly can stifle innovation and creativity.
It also slows down your employees' personal and professional development.
Neglecting Continuous Improvement
When you only rely on cycle time as a metric, you can't make long-term progress. Again, focusing only on quick wins can prevent your team from adjusting and changing.
Remember, to achieve continuous improvement, you need to look beyond cycle time.
Final Words
By focusing on cycle time optimization, I learned how important it is to monitor the time it takes to complete tasks.
Look, being efficient isn't enough; you have to ensure operational excellence and meet customer expectations.
Looking forward, the Cycle Time Formula remains vital for any business. To simplify processes and cut operational expenses, you must understand and apply this formula.
As you apply this knowledge, consider using tools like Apploye. Using it, you can do precise time tracking and workflow management.
With over 100 features, you can monitor, manage, and track for precise cycle time calculations to increase your team's productivity.
Related FAQs about Cycle Time
What measurements can cycle time provide?
When you consider cycle time, you can express it in different units depending on what you provide. Here are some common cycle time measurements —
- Seconds per part
- Parts per second
- Minutes per part
- Parts per minute
- Hours per part
- Parts per hour
How can I track cycle time?
You can track cycle time using a time-tracking platform or project management tool. Tracking cycles is easy with time tracking, detailed reports, Kanban boards, and scheduling.
How do you calculate machine cycle time?
You can calculate machine cycle time by —
- Identifying the start and end points of the operation
- Measuring total production time including processing
- Loading, inspection, unloading, and idle times
- Counting the units produced
- Using the formula —
Machine cycle time = Total production time / Total units produced.
How does cycle time affect production?
Cycle time affects production by increasing efficiency and client satisfaction. A shorter cycle time increases production capacity, reduces lead times, and raises revenue. Faster cycle times mean higher efficiency and customer satisfaction.