What is Operational Efficiency & Strategies to Improve with Examples
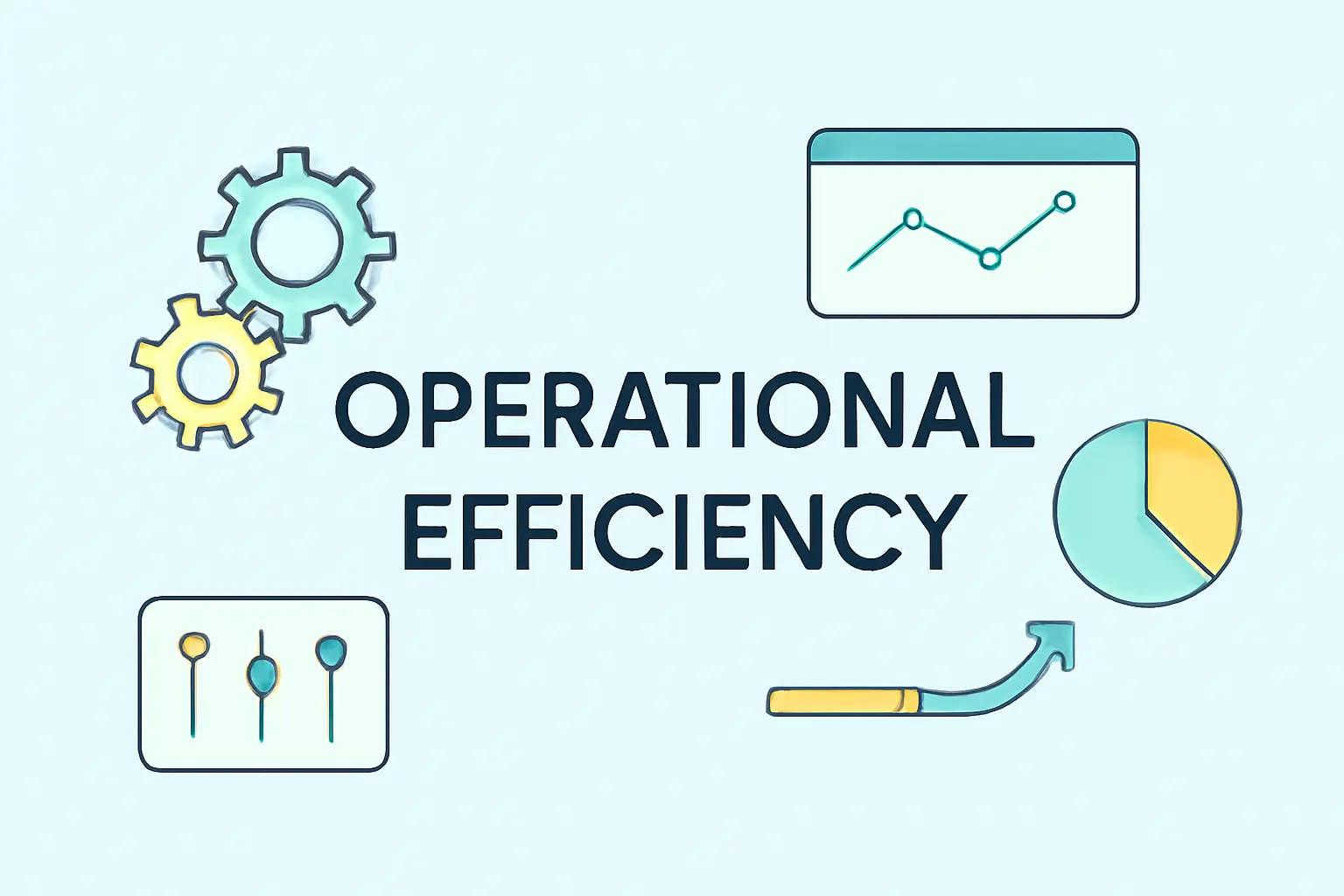
Summary:
-
Operational efficiency is a company’s ability to produce more output with fewer resources.
-
It is important to enhance team productivity, improve the service or product quality, and increase profit margins.
-
Achieve effective operational efficiency through simplifying workflow, using automation & tracking tools, training employees, and monitoring their KPIs.
77% of CEOs are actively pursuing operational efficiencies to drive revenue growth. But most of them fail because they don’t know what it really means, and they just put all their focus on increasing productivity only.
Big mistake!
So, what is operational efficiency, and how do you successfully implement it in your business?
Here, we’ll break down the definition of operational efficiency, show you real-world examples, explore practical strategies to improve it, and clarify how it differs from productivity.
In this article
- What is operational efficiency?
- Operational efficiency vs productivity vs operational effectiveness
- Why operational efficiency is essential
- How do you measure operational efficiency?
- What strategies can increase operational efficiency?
- Best tools for efficiency improvement
What is Operational Efficiency?
Operational efficiency means maximizing the output using as few resources as possible. The real trick lies in optimizing the resources and improving the productivity level.
It is far different from productivity, which focuses on the quantity of output.
But, essentially, the thought behind operational efficiency is concise: “Do more with less.”
That means you want to ensure the best results from the least amount of input. It might include reducing actual costs, removing unnecessary costs, or optimizing operational processes.
All these help to ensure the resources are used effectively.
Remember, operational efficiency is not:
- Using tools for maximizing profit.
- Implementing a single solution and moving on.
- Burdens teams to get more done.
- Random budget cuts without any strategic planning.
- Automating everything blindly.
Operational Efficiency vs Productivity vs Effectiveness (And Why It Matters)
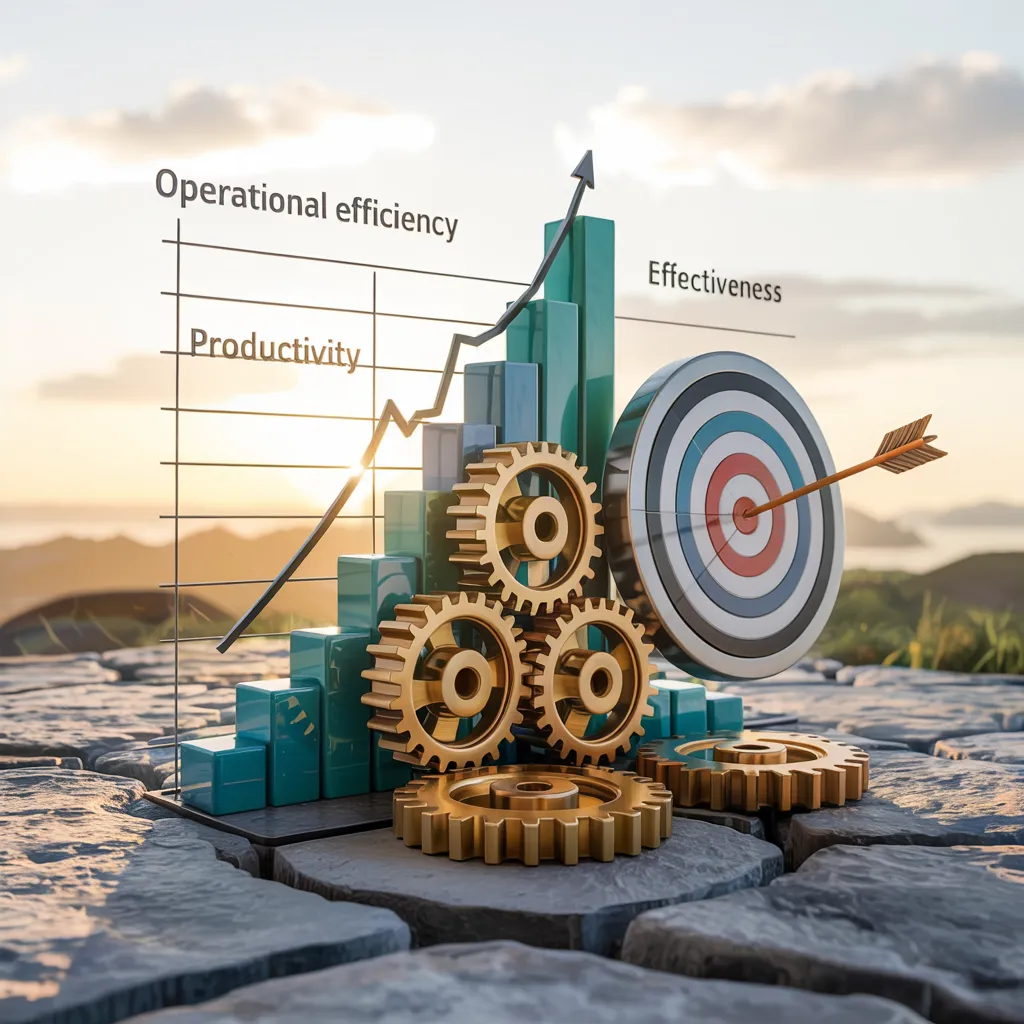
Operational efficiency, effectiveness, and the terms of productivity differ from each other in a few aspects. Here is the clear overview:
Operational Efficiency
The efficiency of operations is mainly about doing things with the right approach. All you want is the desired outcome with the least amount of resources—whether it would be time, money, or effort.
On the motive to reduce cost and waste, efficiency makes the working process automated to produce a given output.
Operational Productivity
Productivity is the measurement of potential output per unit of input.
It refers to the operating efficiency ratio. Like how much you can produce for the amount of resources you use.
And the success is here when all the resources are well converted into output. No matter if it's useful or aligned with business goals.
Track your team's true output potential
Operational Effectiveness
Effectiveness mainly refers to doing the right things. It mainly focuses on the most important tasks to drive the desired outcomes or performance goals.
A business is only effective when it makes the right strategic decisions. Even if they are not always the most efficient for resource use.
Benefits of High Operational Efficiency to Businesses
High operational efficiency saves an organization’s money. As simple as that. However, for a better understanding, let’s have a comprehensive look.
Cost Reduction
The fewer resources used, the less it will cost a company. Operational efficiency achieves just this. Simple work processes bring down labor, materials used, and overhead.
Take inventory management as an example. With an efficient operation, the cost and resource wastage are significantly reduced.
Growth in Profit
When you spend less on production, naturally profit margin grows. Efficiency in
operation directly contributes to this phenomenon. Implementing different techniques, such as employing tracking tools, can achieve this. We’ll explore this more in the later section.
High Employee Morale
According to a recent survey, 76% of employees say workplace culture influences productivity, and 74% link it to better customer service.
Operational efficiency reduces stress by simplifying workflows and clarifying roles. This boosts employee satisfaction.
When staff feel their work is meaningful and well-supported, morale improves.
Customer Contentment
Efficient operations ensure timely, accurate service. It is the key driver of customer satisfaction. By minimizing errors and delays, companies gain customer trust and loyalty.
Efficiency also lets businesses invest more in personalized services and loyalty programs.
The Cost of Operational Inefficiency
Operational inefficiencies have a notable impact on your business. For example:
● Revenue Loss: There is a high chance that companies can lose about 20–30% of their annual revenue due to inefficiencies.
● Manual Processes: Processing the invoice completely manually can cost up to $25 each. And companies are spending a lot on inefficient processes.
● Retail Inefficiencies: Due to inefficiency, retailers can lose an average of 4.5% of revenue.
● Missed Opportunities: Most often, inefficiencies lead to slow responses to market changes.
● Customer Dissatisfaction: Continual delays and mistakes due to inefficiency make the customer frustrated.
● Talent Misallocation: Operational inefficiency often hinders or underutilizes the experts in a company. Even highly skilled team members get slowed down by the administrative tasks.
Stop revenue leaks with smart time tracking!
How to Measure Operational Efficiency
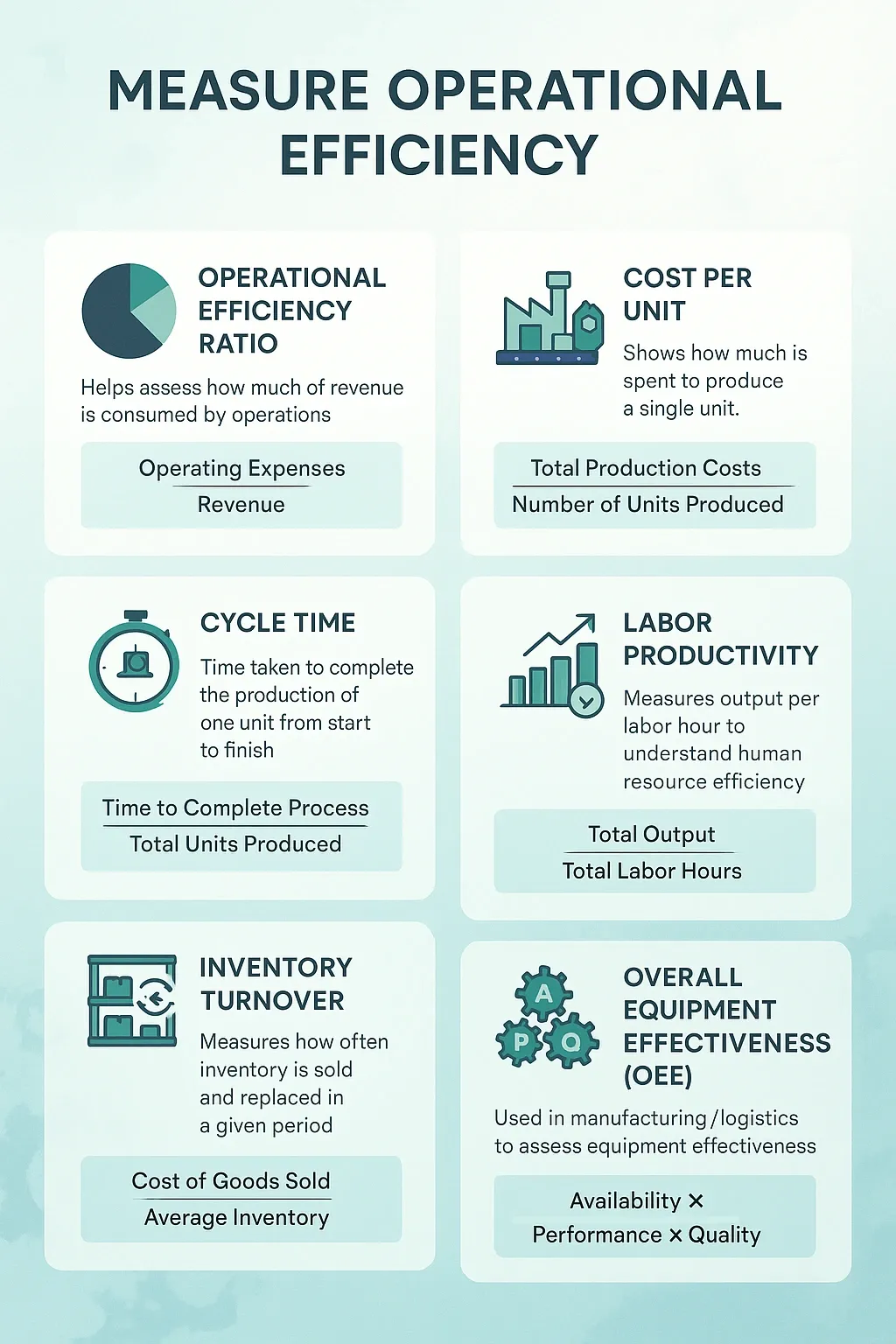
Here are some important KPIs you can consider when tracking operational efficiency:
i) Operational Efficiency Ratio (Operational Expenses vs. Revenue)
The ratio mainly compares a company's operating expenses to its revenue. You can measure how much of the revenue your company consumes by operational costs.
Formula: (Operating Expenses / Revenue)
ii) Cost Per Unit
This measures how much you need to spend to produce one unit of a product or service.
Formula: Total Production Costs / Number of Units Produced
iii) Cycle Time
Cycle time refers to the time duration the company takes to complete one unit of production. Often, businesses use it to measure their process from start to finish and determine how quickly it is completed.
Formula: Time to Complete Process/Total Units Produced
iv) Labor Productivity:
You can use this metric to measure the output per labor hour, highlighting how efficiently labor is being utilized. Business uses this metric when they need to measure how much they spend on human resources.
Formula: Total Output/ Total Labor Hours
Measure employee performance with advanced analytics
v) Inventory Turnover:
The metric finds out how much inventory is sold and replaced over a period. Companies get the complete picture of investment management through this.
Formula: (Cost of Goods Sold / Average Inventory)
vi) Overall Equipment Effectiveness (OEE):
Various manufacturing industries use OEE to measure the effectiveness of machinery and equipment. Businesses track performance, availability, and ensure higher service quality control.
It also applies to sectors like logistics to track the status of equipment used in warehouses.
Formula: Availability×Performance×Quality
What Highly Efficient Operations are Doing Differently (Examples)
Go through some expert insights to learn what they mean by operational efficiency:
“Quality is a result. Lean and Six Sigma are about identifying the critical drivers and root causes of quality results.”
— Thomas Pyzdek, Lean Six Sigma Consultant
Here, Pyzdek advocates for a strategic approach named Lean and Six Sigma methodologies. These help to diminish the underlying causes that affect operational excellence.
“We’re always working on the supply chain. We’re always trying to make it better.”
— Tim Cook, Former COO and Current CEO of Apple
Here, Tim Cook is clear, highlighting the importance of continuous improvement. It is the best use of the options to achieve excellence in operational effectiveness.
“The most dangerous kind of waste is the waste we do not recognize.”
— Shigeo Shingo, Lean Management Expert
He meant the hidden inefficiencies, like untracked time, unnecessary steps, or unnoticed delays. They are truly harmful to the current operations. Due to ignorance, it silently drains the energy of employees and reduces productivity.
“Work simplification is the organized use of common sense by everyone involved to find easier and better ways of doing work.”
— Allan H. Mogensen, Father of Work Simplification
Here, Mogensen focuses on collective effort to identify practical improvements to enhance business efficiency.
5 Best Ways To Measure Productivity
How to Improve Operational Efficiency
Here are five proven strategies you can use to enhance efficiency:
1. Simplify Current Processes Using Lean/Six Sigma
These two renowned methodologies are used for cost savings and improving operational performance. You can reduce delays, eliminate waste, and ensure that resources are spent only on value-creating activities. This helps you to drive productivity.
Tactics:
- Value Stream Mapping: Helps in process mapping and tracks down all the steps to find which add value and which don’t.
- Kaizen: Invite the employees at all stages to share their valuable ideas for change or improvement.
- DMAIC: Apply Six Sigma’s DMAIC method and find out process inefficiencies.
Update your workflow in minutes with Apploye!
2. Use Automation and Technology
You can apply some advanced technologies, like RPA, Artificial Intelligence, or ERP (Enterprise Resource Planning) systems. It automates repetitive tasks, centralizes data, and improves organizational efficiencies.
You can reduce errors, speed up workflows, and help employees focus on higher-level activities.
Tactics:
- RPA to Automate Routine Tasks: Automate data entry, invoicing, and basic customer service queries.
- AI-powered Decision Making: Use AI to predict customer demand, optimize supply chains, and personalize customer interactions.
- ERP Integration: Connect an ERP system for operations optimization at different business functions.
20 Time Tracking Best Practices Guide
3. Improve Training and Employee Engagement
Well-trained and knowledgeable employees are key to operating efficiently. Through training, you can make them productive, problem solvers, and adaptive to processes in any situation.
Tactics:
- Upskilling and Reskilling: Train them to ensure they can best use the tools, technologies, and methodologies.
- Cross-Training: Allow the employees to learn different roles and increase flexibility in workflows.
- Employee Empowerment: Must involve them in decision-making and process improvements.
4. Apply Data Analytics and Track KPIs
Measuring your project performance with effective KPIs is important to identify trends, diminish inefficiencies. You can take the right actions before the problems escalate.
For this, all you need to do is:
- Install predictive analytics and track demand, and optimize inventory
- Measure financial performance with cycle time, cost per unit, and employee productivity, and find areas for improvement
- Use real-time data dashboards to visualize KPIs and track progress
5. Outsource Non-Core Activities to Specialists
Assigning responsibility for company operations also does not just stick to central experts. You need to ensure flexible and practical outsourcing of some tasks to experts for specialized functions.
It is a far more effective approach for managing complex IT systems or payroll processes in-house. You can outsource customer support, accounting, or logistics tasks to experts and manage operational performance.
It helps reduce direct costs, improve speed, and in-house team to focus on important tasks.
Best Tools to Increase Operational Efficiency
1. Project Management Tools
- Apploye – Apploye is a task management tool to keep the team on track through automated workflows and detailed timelines. You can assign tasks, set deadlines, and track progress in real-time. With automation, it ensures projects stay on schedule with improved productivity.
- Trello – The Trello project management tool offers Kanban-style boards to visually organize tasks. It helps teams move tasks across columns such as To-Do, In Progress, and Done. It makes task tracking easier and maintains deadlines.
- Jira – Jira is mainly designed for agile operations, particularly in software development. Get the DBA features, including Scrum boards, customizable workflows, and backlog management. Through these, teams can break down projects into manageable sprints.
Organize your team with the right tools!
2. Workflow Automation Tools
- Zapier – It is the most popular no-code platform that helps connect thousands of apps and create automated workflows called "Zaps." You can set triggers and actions between apps. Like, you can automatically move data from one app to another.
- Power Automate – It is Microsoft’s workflow automation tool that integrates with Office 365 and other Microsoft products. The user can automate workflows and repetitive tasks. With RPA, it is now easier to handle more complex business flow automation.
Top 11 Benefits of Employee Monitoring
3. Inventory and Supply Chain Management Tools
- Oracle NetSuite – It is a cloud-based ERP platform that offers all the advanced inventory and supply chain management features. You will get real-time tracking of inventory levels, automated reordering, and demand planning. With integration, you can optimize procurement and production processes.
- SAP SCM – SAP SCM is a supply chain management tool that is designed for large enterprises. It offers advanced features for supply chain planning, execution, and monitoring.
- Zoho Inventory – It is a cloud-based inventory management tool used by small and medium-sized businesses. Businesses can manage stock across multiple sales channels, track shipments, and automate stock updates.
4. Customer Service and Support Tools
- Zendesk – Zendesk offers an omnichannel customer support platform through multiple communication channeLikelike as email, chat, social media, and voice. You can manage customer queries through a single ticketing system.
- Salesforce Service Cloud – You can use this cs platform with Salesforce’s CRM built in. It offers advanced tools to manage customer inquiries, cases, and support tickets.
5. Internal Communication and Collaboration Tools
- Slack – Use Slack to communicate in channels, either by department, project, or topic. It offers real-time messaging, file sharing, and integrations with hundreds of other apps.
- Microsoft Teams – It offers chat, video calls, file sharing, and other tools within the Office 365 ecosystem. Organizations use this tool to chat in channels, hold virtual meetings, or collaborate on documents.
6. Business Intelligence (BI) and Analytics Tools
- Tableau – This renowned BI tool comes with all the advanced data visualization features. You can build interactive and shareable dashboards. Here you can represent data and identify trends and areas for BI improvement.
- Power BI – If you want a cost-effective BI tool, go with Power BI, developed by Microsoft. Through Microsoft Office integration, you can analyze complex data and manage reports.
7. HR and Employee Productivity Tools
- BambooHR – This HR software is suitable for medium-sized businesses. You will find an intuitive interface to manage employee data and review performance.
- ADP Workforce Now – Looking for an integrated platform to manage HR, payroll, or compliance? ADP Workforce Now is a perfect solution, especially for mid-to-large businesses.
8. Financial Management and Accounting Tools
- QuickBooks Online – It is a cloud-based accounting solution for small and medium-sized businesses. You’ll find tools to manage invoices, expenses, payroll, and taxes.
- Oracle NetSuite (Financials) – You will get an ERP system with advanced financial management features with this finance suite. Mid-to-large enterprises can use this to optimize their financial tasks.
- Sage Intacct – It is a cloud-based accounting software suitable for growing businesses and organizations. It offers tools like multi-entity management, project accounting, and financial analysis.
How Apploye Improves Your Operational Efficiency
So, if you are planning to improve operational efficiency rate with one of the best time tracking and employee monitoring tools, Apploye can help. Here's how it aligns with these strategies:
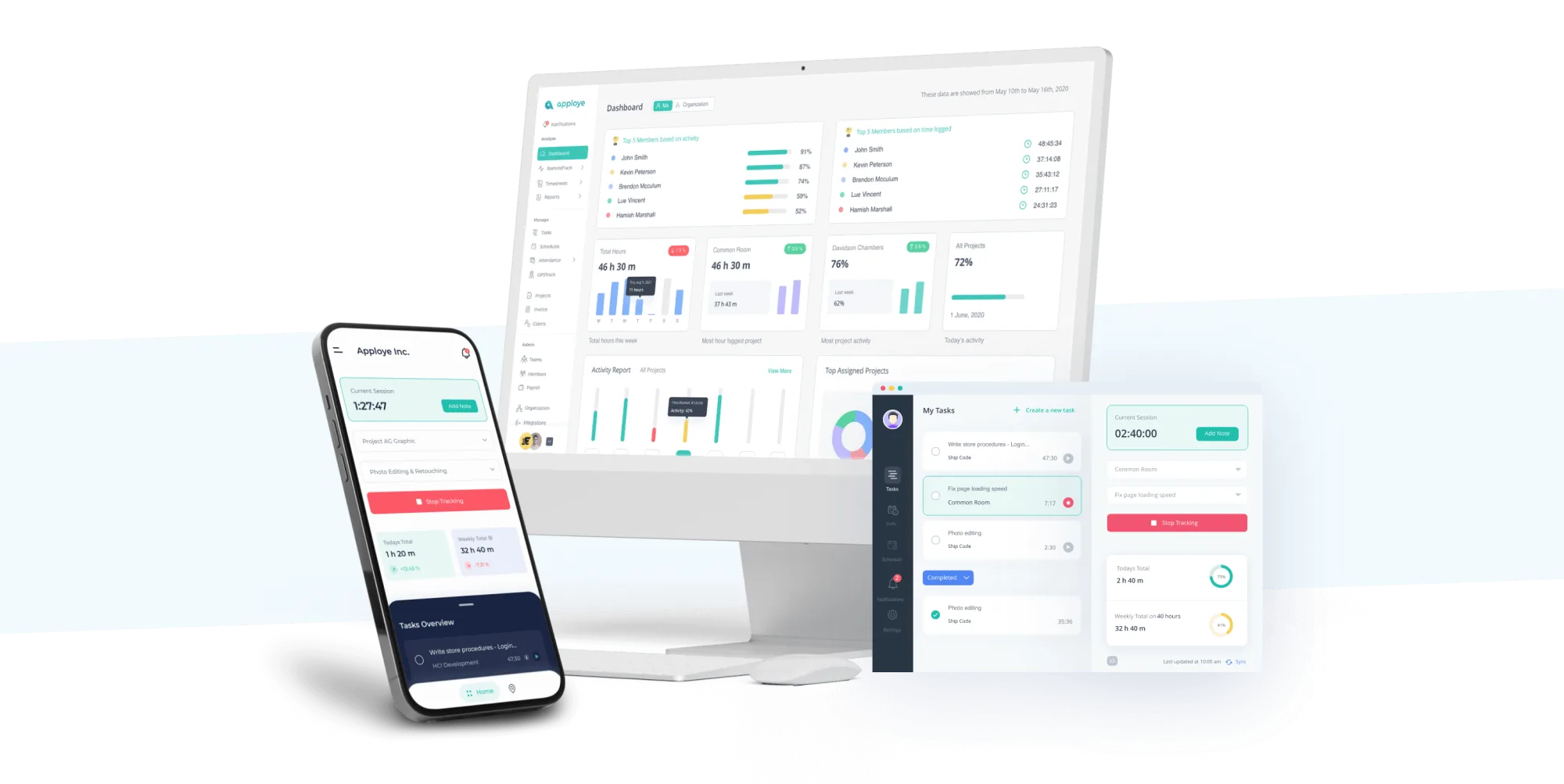
Simplify Processes and Eliminate Waste (Lean Operations)
Apploye provides features to track employee activity. Managers can identify inefficiencies like idle time or delays. With real-time data collection, you can adjust your business strategy and ensure the projects are completed without any distractions.
Leverage Auto-tracking Technology
Apploye can track employee hours without manual involvement. You can generate reports and send invoices according to the tracked time. With some advanced features like automatic time tracking, reminders, and activity monitoring, businesses can handle the common tasks more easily now.
Enhance Employee Training and Engagement
With Apploye, you get a clear overview of work hours and productivity levels. By tracking the lacking employee skills, you can enroll them for additional training.
Use Data Analytics and KPIs for Continuous Improvement
Apploye offers valuable insights into employee productivity. Organizations get detailed reports and analytics. Plus, with tracking operational KPIs, you can find out areas for improvement.
Focus on Core Competencies (Outsourcing Non-Core Activities)
After streamlining operations, teams can focus on core competencies. That’s the point—they can outsource non-core business activities to external specialists. It frees up the internal resources for strategic initiatives and finds areas for further improvement.
Best Employee Time Tracking Software
Conclusion
Operational efficiency is not all about what you will get overnight. All you need to be is strategic and careful with your work planning. Plus, invest in proper time management and operations optimization software.
Start your efficiency journey now!
Frequently Asked Questions about Operational Efficiency
Q: What does operational efficiency mean for a business?
A: Operational efficiency defines how much a business can deliver products or services at the lowest cost. This includes process automation and waste reduction to maximize ROI on operations.
Q: What are the 3 factors of operational efficiency?
A: The three main factors of operational efficiency in business are process optimization, resource management, and technology use. Process optimization improves workflows, while resource management ensures the best use of resources. Technology helps reduce manual work through automation and tools.
Q: What are examples of operational efficiency?
A: Some common examples are automating repetitive tasks and, best use of resources. Also, it includes optimizing supply chain logistics and having cost reduction strategies to ensure a higher return.
Q: What distinguishes operational efficiency from operational excellence?
A: Operational efficiency is about doing tasks with minimal resources and time. Operational excellence, on the other hand, goes beyond efficiency. It aims for continuous improvement and high-quality outcomes.
Q: What to improve first: efficiency or productivity?
A: It’s usually best to focus on process efficiency first, as improving efficiency helps you do more with the resources you already have. Once efficiency is done, you can focus on improving productivity and increasing the amount of production.
Q: How to diagnose operational efficiency problems?
A: To diagnose operational efficiency problems, review the key performance wth the KPIs like production time, cost, and resource usage. You can conduct thorough audits to find the bottlenecks, delays, or waste. Then adjust your efficiency strategy based on the data collected.
Q: What are the benefits of operational efficiency for businesses and customers?
A: Businesses can lower expenses, streamline processes, and enhance their overall performance. Customers can ensure high-quality products on time with minimal resource usage and without wasting time. It results in a higher customer satisfaction level, and the company can reach its goals.
Q: How can businesses improve operational efficiency without cutting costs?
A: Through optimizing workflows with technologies, improving employee training, or increasing resource allocation, businesses can improve operational efficiency without spending too much.
Q: How does lean manufacturing improve operational efficiency?
A: Lean process helps to systematically identify and eliminate waste in processes. It reduces cost and helps teams to be more productive.
Q: How can technology improve operational efficiency?
A: Technology has a big part in automating repetitive tasks, streamlining processes. Some digital tools like ERP systems, AI-powered analytics, and RPA help minimize manual efforts and save time. You can improve the overall workflow, resulting in efficient operations.
Q: How can we improve the financial efficiency of our business operations?
A: To improve financial efficiency, cut down on the additional cost. Use the related technologies and review your pricing strategies. Invest in automation to minimize manual work and optimize cash flow management.